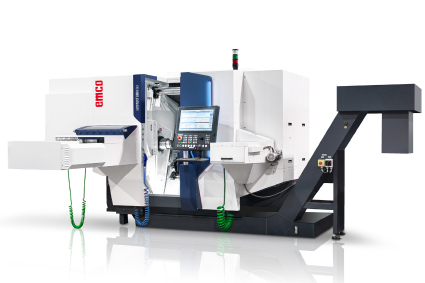
Dotata di serie di un mandrino Bigbore 51, l’Hyperturn 50 ha una maggiore capacità di barra per una maggiore flessibilità nella lavorazione delle barre. Inoltre, la potenza di azionamento di 8,8 kW e 12.000 giri/min consente di eseguire potenti operazioni di fresatura, anche su materiali d'acciaio impegnativi. Va da sé che l’Hyperturn 50 dispone anche della tecnologia di controllo all'avanguardia di FANUC con il FANUC 31i-B Plus o Sinumerik ONE, entrambi con interfaccia utente EMCONNECT.
L'HT50 può essere automatizzato con diversi alimentatori di barre o con un caricatore orientabile EMCO, un caricatore a portale EMCO o il Robojob Turn-Assist per l'alimentazione dei pezzi.
L'Hyperturn 50 convince grazie all'ampia distanza tra i mandrini di 760 mm per una lavorazione senza collisioni con due torrette. L'area di lavoro ampliata offre spazio sufficiente per l'integrazione di torrette BMT nelle versioni a 12 o 16 posizioni. Grazie all'interfaccia di precisione per una preparazione rapida e all'azionamento diretto per la fresatura ad alte prestazioni di pezzi complessi, questa soluzione è di prima scelta. L'azionamento diretto raffreddato ad acqua eroga 8,8 kW, fora e fresa fino a 12.000 giri/min e consente una coppia di 20 Nm. L'interfaccia BMT, stabile e precisa, garantisce una lunga durata dell'utensile. In definitiva, l'utente ha a disposizione più opzioni per la lavorazione dei pezzi e per aumentare la produttività.
Struttura della macchina
Il basamento inclinato a 72° costituisce il cuore della macchina. Progettato come una struttura in acciaio saldato estremamente rigida e compatta, costituisce la base per un tornio robusto e preciso. I rinforzi forniscono ulteriore rigidità nelle aree soggette a maggiori sollecitazioni. L'uso dell'acciaio al posto della tradizionale fusione della macchina offre vantaggi in termini di rigidità e di comportamento termico del tornio durante la fase di riscaldamento. Tutte le guide sono progettate come guide a rulli precaricate. Queste sono fissate su superfici di supporto accuratamente lavorate e sigillate con strisce di copertura in acciaio per evitare la contaminazione. Le coperture fisse in acciaio inox nell'area di lavoro aumentano la sicurezza operativa e la durata.
Mandrino principale/contro-mandrino:
L'elevata potenza di azionamento dei mandrini, abbinata a caratteristiche di coppia ottimali, garantisce un'elevata economicità nella lavorazione dell'acciaio e nella lavorazione ad alta velocità dell'alluminio. I motori mandrino integrati (ISM), montati su cuscinetti di precisione di grandi dimensioni, consentono una gamma di velocità particolarmente ampia, abbinata a proprietà di concentricità estremamente buone. Le testate simmetriche, insieme ai sensori di temperatura nei punti di appoggio e al raffreddamento a liquido, garantiscono un'elevata stabilità termica.
Sull'Hyperturn 50, la contropunta del mandrino poggia su una propria guida a rulli e può essere spostata automaticamente su una lunghezza di 510 mm. Un espulsore dei pezzi controllato dalla corsa, inondato di refrigerante, garantisce una rimozione sicura dei pezzi finiti. Su richiesta, il cilindro di bloccaggio completo può essere sostituito da un cilindro di bloccaggio cavo con un foro passante di 45 mm di diametro per scambiare pezzi ad albero lungo con il contromandrino.
Dotata dei più recenti sistemi di controllo e azionamento - Sinumerik ONE o Fanuc 31i-B Plus con EMCONNECT - la macchina può essere programmata in modo semplice ed efficace. Il nuovo pannello di controllo, regolabile in altezza e girevole, offre una migliore ergonomia, soprattutto se la programmazione viene effettuata in macchina. Nel design della macchina è stata inoltre integrata una barra di stato a LED multicolore di nuova concezione, per visualizzare all'operatore gli stati delle singole operazioni.
EMCONNECT
EMCONNECT è l'acronimo di connettività e collegamento in rete dell'ambiente di produzione ed è un assistente di processo digitale per l'integrazione completa di applicazioni specifiche del cliente e del sistema relative al controllo delle macchine e al processo di produzione. L'utente e le sue esigenze sono al centro dei processi operativi: l'obiettivo è rendere i processi di lavoro più efficienti e mantenere la consueta elevata affidabilità delle macchine in tutte le modalità operative.
Con EMCONNECT, l'utente ha accesso a importanti funzioni aggiuntive direttamente dal pannello di controllo.
Ciò significa che tutte le informazioni, i dati e i sistemi importanti possono essere consultati direttamente e centralmente sulla macchina. Grazie al sistema modulare di Emco, è possibile implementare con particolare flessibilità anche applicazioni specifiche per i progetti e i clienti. EMCONNECT è quindi la chiave per ottimizzare i processi di lavoro e aumentare la produttività.
La selezione di applicazioni disponibili viene costantemente ampliata. Ad esempio, è ora disponibile l'opzione Shopfloor Data per l'acquisizione dei dati di macchina e di produzione (MDA/PDA). Consente il monitoraggio completo di tutte le macchine e l'organizzazione dei processi nell'area di produzione. Questo prodotto si distingue in particolare per l'indipendenza dalle macchine e dai produttori e per l'accesso mobile allo stato delle macchine tramite smartphone o tablet. Attualmente è in preparazione il servizio dati EMCONNECT per una manutenzione preventiva mirata che riduce al minimo i tempi di fermo macchina.